Volltextsuche nutzen
- versandkostenfrei ab € 30,–
- 6x in Wien und Salzburg
- 6 Mio. Bücher
- facultas
- Detailansicht
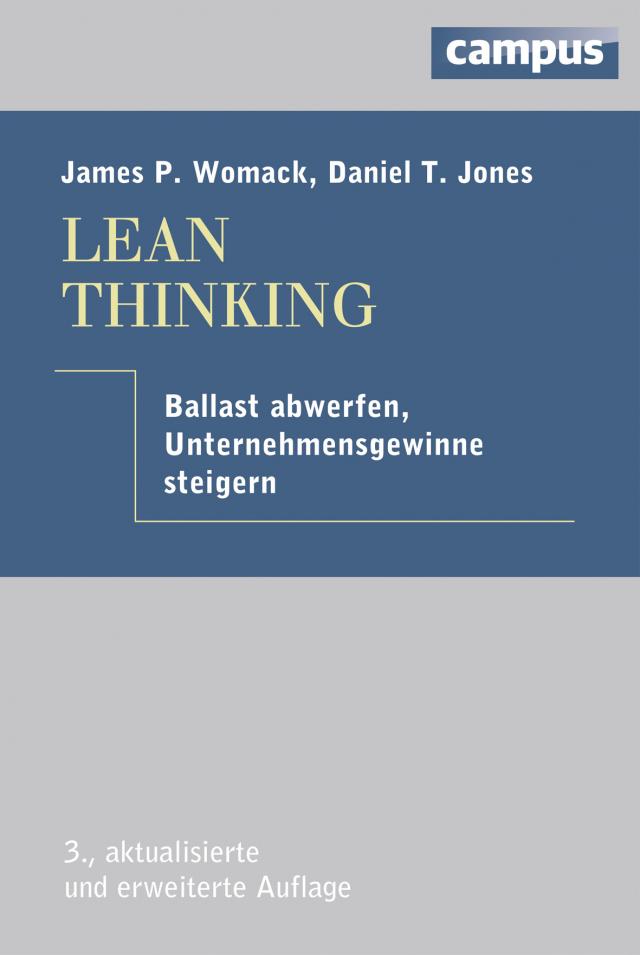
Lean Thinking
Ballast abwerfen, Unternehmensgewinn steigern
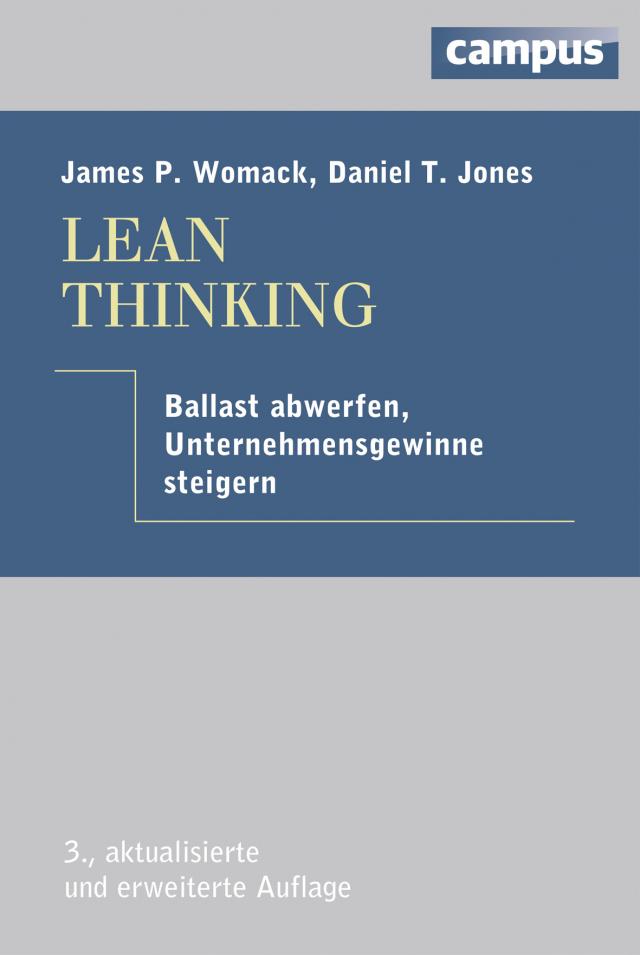
Hardcover
59,70€
inkl. gesetzl. MwSt.
Besorgungstitel
Lieferzeit 1-2 WochenVersandkostenfreibestellen in Österreich
Lieferzeit 1-2 WochenVersandkostenfreibestellen in Österreich
Deutschland: € 10,00
EU & Schweiz: € 20,00
EU & Schweiz: € 20,00
In den Warenkorb
Click & Collect
Artikel online bestellen und in der Filiale abholen.
Derzeit in keiner facultas Filiale lagernd. Jetzt online bestellen!Artikel online bestellen und in der Filiale abholen.
Artikel in den Warenkorb legen, zur Kassa gehen und Wunschfiliale auswählen. Lieferung abholen und bequem vor Ort bezahlen.
Auf die Merkliste
Veröffentlicht 2013, von James P. Womack, Daniel T. Jones bei Campus, FreePress, New York
ISBN: 978-3-593-39843-3
Auflage: 3. Auflage
444 Seiten
66 Abbildungen, 11 Tabellen
23.2 cm x 16.1 cm
Der Erfolg in der Praxis zeigt: Lean Thinking macht aus den einzelnen Unternehmensbereichen, die am Produktionsprozess beteiligt sind, ein hoch effizientes Netzwerk, das so dicht wie möglich am Kunden arbeitet. An zahlreichen Beispielen von erfolgreichen Unternehmen aus verschiedenen Kontinenten zeigen die Autoren, wie die fünf Grundprinzipien des Lean Thinking umsetzbar sind und wie man mit ...
Werbliche Überschrift
»Ein brillant geschriebenes Werk« FTD
Textauszug
Vorwort der Autoren zur 3. Auflage
Vor der Rezession in Europa und dem nachlassenden Wachstum Chinas ist auch die boomende deutsche Exportwirtschaft nicht gefeit. Damit gewinnt dieses Buch zusätzliche Aktualität. Wann immer die deutsche Industrie sich in den letzten zwei Jahrzehnten vor schwierige Herausforderungen gestellt sah, wiesen ihr die ›leanen‹ Maßnahmen, die in diesem Buch geschildert werden, den Weg nach vorne. Da der Weg zur Verbesserung, den es schildert, eine unendliche Aufgabe darstellt, finden sich immer neue Pfade, durch effektivere Zusammenarbeit Kundenbedürfnisse zu befriedigen und Arbeitsplätze zu sichern.
Unser früheres Buch, Die zweite Revolution in der Autoindustrie, erschien 1992, zu einem Zeitpunkt, da der Automobilabsatz erstmals seit Jahrzehnten zurückging und die deutsche Vorherrschaft im Luxussegment angesichts der Markteinführung des Lexus aus dem Toyota-Konzern ins Wanken geriet. Es war ein Weckruf, der in Wolfsburg, München und Stuttgart ebenso laut und deutlich zu hören war wie in Detroit. Und es sorgte für Unruhe bei Gewerkschaften in vielen Ländern, wo man fürchtete, lean thinking werde zum Abbau von Arbeitsplätzen und zu einem Machtverlust der Gewerkschaften führen. In Deutschland kam es anders.
Als Wendelin Wiedeking 1992 vor der Aufgabe stand, den legendären Sportwagenhersteller Porsche zu retten, las er Die zweite Revolution in der Autoindustrie und engagierte zu seiner Unterstützung eine Handvoll erfahrener Sensei von Toyota. Diese begannen unverzüglich damit, den bei Porsche tief verwurzelten Handwerksgeist infrage zu stellen. Ferner begannen sie, vom Arbeiter über den Ingenieur bis hin zum Manager alle Mitarbeiter in einen Prozess einzubinden, dessen Ziel es war, die Arbeitsabläufe bei der Autoherstellung leaner zu gestalten. Dr. Wiedeking blickte auch zu Toyota, Honda und BMW, um zu lernen, wie man Autos entwirft, die gleich im ersten Lauf schlüsselfertig montiert werden, um so die damals in deutschen Autofabriken verbreiteten Feinschliff- und Anpassungsarbeiten überflüssig zu machen.
Wir trafen just in dem Augenblick ein, da der erste perfekte Porsche vom Band rollte. Von vielen Mitarbeitern hörten wir, dass die neuen Prozesse auf dramatische Weise die Augen für eine andere Arbeitsweise geöffnet hatten. Damit war für uns der Beweis erbracht, dass sich mit lean thinking auch in Deutschland Erfolge feiern ließen, nicht nur in Japan. Diese Geschichte haben wir in unserem Buch Lean Thinking ausführlich geschildert, um sie in der deutschen Wirtschaft bekannt zu machen. Porsches andauerndes Wachstum führte das Unternehmen an einen Punkt, an dem es sich gar zur Übernahme des riesigen Volkswagen-Konzerns imstande fühlte. Damit hatte man sich überhoben, doch selbst nach der anschließenden Übernahme durch VW geht Porsche innerhalb der Unternehmensgruppe mit den Prinzipien des lean thinking voran.
Die nächste Herausforderungen konkretisierten sich ein Jahrzehnt später, in Gestalt der Globalisierung des herstellenden Gewerbes und des Aufstiegs Chinas als Produktionsstandort. Überall sah sich die Industrie unter Druck, Produktion und Arbeitsplätze aus Hochlohnländern wie Deutschland abzuziehen. Doch das Beispiel Porsche zeigte, dass die Einführung leaner Arbeitsweisen im Einvernehmen mit der Belegschaft eine Alternative darstellte. In ganz Deutschland einigten sich Gewerkschaften und Arbeitgeber, in Sachen Lohnforderungen und Arbeitszeiten Mäßigung walten zu lassen und die Produktivität mit lean practices zu steigern, wodurch sowohl Arbeitsplätze als auch das mit ihnen verbundene Wissen im Land blieben. Auf diesem Fundament ließ sich aufbauen, als die Exportnachfrage wieder anzog.
Was bei Porsche noch eine Schocktherapie gewesen war, konnte in Form von Aus- und Weiterbildungen in der Anwendung leaner Werkzeuge und Techniken in ganz Deutschland fortgesetzt werden. Doch es zeigte sich bald, dass es zu ihrer wirklichen Effektivität auch eines neuen Management-Systems bedurfte. Dementsprechend entwickelte Bosch auf Grundlage der von Toyota erlernten schlanken Prinzipien sein Bosch Production System. Im Laufe des nächsten Jahrzehnts wurde so das Management der weltweiten Produktionsstandorte auf Vordermann gebracht.
Unter Anwendung schlanker Prinzipien wurde auch ein Bosch Engineering System entwickelt, mit dem die Entwicklung von Produkten und Herstellungswerkzeugen von einem neuen Ansatz her gedacht wurde. Zuvor hatte Bosch seine Meisterschaft in der Entwicklung großer, teurer und technisch ausgefeilter automatischer Systeme bewiesen. Doch man musste feststellen, dass solch teure Systeme nicht mehr zukunftsfähig waren. Um an ihre Stelle zu treten, entwarf man eine neue Palette kleinerer und klügerer, optimal dimensionierter Werkzeuge, die mühelos an veränderte Umstände angepasst werden konnten und sogar global beweglich waren, um dem Lebenszyklus des Produkts auf Schritt und Tritt folgen zu können. Schließlich fanden diese leanen Praktiken auch in den Bereichen Planung, Logistik, Verwaltung und Vertrieb Anwendung und fügten sich zum Bosch Business System zusammen. Viele andere deutsche Unternehmen folgen dem Beispiel Boschs.
Die lean practices zu vertiefen, um die kommenden Herausforderungen zu meistern, heißt auch, über Werkshalle und Konstruktionsbüro hinauszublicken und neue Wege, ein leanes Unternehmen zu führen, zu gehen. In den vergangenen Jahren hatten wir die Gelegenheit, einige ganz neue Werkzeuge zum lean management und neue Verhaltensweisen des lean leader ship kennenzulernen. Dazu gehört etwa Hoshin Kanri, eine strategische Herangehensweise, mit der Optimierungsbemühungen effektiver auf die wesentlichen Problembereiche konzentriert werden können. Ferner wäre die Value Stream Analysis zu nennen, mit deren Hilfe die horizontalen Arbeitsströme über Abteilungen hinweg neu ausgerichtet werden können - denn diese Arbeitsströme sind es, welche die Werte erzeugen, für die der Kunde zahlt. Schließlich fallen in diese Kategorie auch A3 Thinking und Toyota Kata, mit denen sich die Anwendung einer wissenschaftlichen Denkweise auf allen Unternehmensebenen durchsetzen lässt. Diese und andere Werkzeuge in einer offenen, visuellen Umgebung zur Anwendung zu bringen, in der Schwierigkeiten und Widersprüche nicht unter den Teppich gekehrt werden, stellt für die in vertikalen Strukturen verhafteten deutschen Unternehmen eine besondere Herausforderung dar.
Beschreibung
Der Erfolg in der Praxis zeigt: Lean Thinking macht aus den einzelnen Unternehmensbereichen, die am Produktionsprozess beteiligt sind, ein hoch effizientes Netzwerk, das so dicht wie möglich am Kunden arbeitet. An zahlreichen Beispielen von erfolgreichen Unternehmen aus verschiedenen Kontinenten zeigen die Autoren, wie die fünf Grundprinzipien des Lean Thinking umsetzbar sind und wie man mit ihnen Produkte und Prozesse optimiert. In dieser neuen Auflage gehen die Autoren in einem exklusiven Beitrag auf die Erfolgsgeschichte von Lean Management in Deutschland ein.
»Ein brillant geschriebenes Werk« FTD
Textauszug
Vorwort der Autoren zur 3. Auflage
Vor der Rezession in Europa und dem nachlassenden Wachstum Chinas ist auch die boomende deutsche Exportwirtschaft nicht gefeit. Damit gewinnt dieses Buch zusätzliche Aktualität. Wann immer die deutsche Industrie sich in den letzten zwei Jahrzehnten vor schwierige Herausforderungen gestellt sah, wiesen ihr die ›leanen‹ Maßnahmen, die in diesem Buch geschildert werden, den Weg nach vorne. Da der Weg zur Verbesserung, den es schildert, eine unendliche Aufgabe darstellt, finden sich immer neue Pfade, durch effektivere Zusammenarbeit Kundenbedürfnisse zu befriedigen und Arbeitsplätze zu sichern.
Unser früheres Buch, Die zweite Revolution in der Autoindustrie, erschien 1992, zu einem Zeitpunkt, da der Automobilabsatz erstmals seit Jahrzehnten zurückging und die deutsche Vorherrschaft im Luxussegment angesichts der Markteinführung des Lexus aus dem Toyota-Konzern ins Wanken geriet. Es war ein Weckruf, der in Wolfsburg, München und Stuttgart ebenso laut und deutlich zu hören war wie in Detroit. Und es sorgte für Unruhe bei Gewerkschaften in vielen Ländern, wo man fürchtete, lean thinking werde zum Abbau von Arbeitsplätzen und zu einem Machtverlust der Gewerkschaften führen. In Deutschland kam es anders.
Als Wendelin Wiedeking 1992 vor der Aufgabe stand, den legendären Sportwagenhersteller Porsche zu retten, las er Die zweite Revolution in der Autoindustrie und engagierte zu seiner Unterstützung eine Handvoll erfahrener Sensei von Toyota. Diese begannen unverzüglich damit, den bei Porsche tief verwurzelten Handwerksgeist infrage zu stellen. Ferner begannen sie, vom Arbeiter über den Ingenieur bis hin zum Manager alle Mitarbeiter in einen Prozess einzubinden, dessen Ziel es war, die Arbeitsabläufe bei der Autoherstellung leaner zu gestalten. Dr. Wiedeking blickte auch zu Toyota, Honda und BMW, um zu lernen, wie man Autos entwirft, die gleich im ersten Lauf schlüsselfertig montiert werden, um so die damals in deutschen Autofabriken verbreiteten Feinschliff- und Anpassungsarbeiten überflüssig zu machen.
Wir trafen just in dem Augenblick ein, da der erste perfekte Porsche vom Band rollte. Von vielen Mitarbeitern hörten wir, dass die neuen Prozesse auf dramatische Weise die Augen für eine andere Arbeitsweise geöffnet hatten. Damit war für uns der Beweis erbracht, dass sich mit lean thinking auch in Deutschland Erfolge feiern ließen, nicht nur in Japan. Diese Geschichte haben wir in unserem Buch Lean Thinking ausführlich geschildert, um sie in der deutschen Wirtschaft bekannt zu machen. Porsches andauerndes Wachstum führte das Unternehmen an einen Punkt, an dem es sich gar zur Übernahme des riesigen Volkswagen-Konzerns imstande fühlte. Damit hatte man sich überhoben, doch selbst nach der anschließenden Übernahme durch VW geht Porsche innerhalb der Unternehmensgruppe mit den Prinzipien des lean thinking voran.
Die nächste Herausforderungen konkretisierten sich ein Jahrzehnt später, in Gestalt der Globalisierung des herstellenden Gewerbes und des Aufstiegs Chinas als Produktionsstandort. Überall sah sich die Industrie unter Druck, Produktion und Arbeitsplätze aus Hochlohnländern wie Deutschland abzuziehen. Doch das Beispiel Porsche zeigte, dass die Einführung leaner Arbeitsweisen im Einvernehmen mit der Belegschaft eine Alternative darstellte. In ganz Deutschland einigten sich Gewerkschaften und Arbeitgeber, in Sachen Lohnforderungen und Arbeitszeiten Mäßigung walten zu lassen und die Produktivität mit lean practices zu steigern, wodurch sowohl Arbeitsplätze als auch das mit ihnen verbundene Wissen im Land blieben. Auf diesem Fundament ließ sich aufbauen, als die Exportnachfrage wieder anzog.
Was bei Porsche noch eine Schocktherapie gewesen war, konnte in Form von Aus- und Weiterbildungen in der Anwendung leaner Werkzeuge und Techniken in ganz Deutschland fortgesetzt werden. Doch es zeigte sich bald, dass es zu ihrer wirklichen Effektivität auch eines neuen Management-Systems bedurfte. Dementsprechend entwickelte Bosch auf Grundlage der von Toyota erlernten schlanken Prinzipien sein Bosch Production System. Im Laufe des nächsten Jahrzehnts wurde so das Management der weltweiten Produktionsstandorte auf Vordermann gebracht.
Unter Anwendung schlanker Prinzipien wurde auch ein Bosch Engineering System entwickelt, mit dem die Entwicklung von Produkten und Herstellungswerkzeugen von einem neuen Ansatz her gedacht wurde. Zuvor hatte Bosch seine Meisterschaft in der Entwicklung großer, teurer und technisch ausgefeilter automatischer Systeme bewiesen. Doch man musste feststellen, dass solch teure Systeme nicht mehr zukunftsfähig waren. Um an ihre Stelle zu treten, entwarf man eine neue Palette kleinerer und klügerer, optimal dimensionierter Werkzeuge, die mühelos an veränderte Umstände angepasst werden konnten und sogar global beweglich waren, um dem Lebenszyklus des Produkts auf Schritt und Tritt folgen zu können. Schließlich fanden diese leanen Praktiken auch in den Bereichen Planung, Logistik, Verwaltung und Vertrieb Anwendung und fügten sich zum Bosch Business System zusammen. Viele andere deutsche Unternehmen folgen dem Beispiel Boschs.
Die lean practices zu vertiefen, um die kommenden Herausforderungen zu meistern, heißt auch, über Werkshalle und Konstruktionsbüro hinauszublicken und neue Wege, ein leanes Unternehmen zu führen, zu gehen. In den vergangenen Jahren hatten wir die Gelegenheit, einige ganz neue Werkzeuge zum lean management und neue Verhaltensweisen des lean leader ship kennenzulernen. Dazu gehört etwa Hoshin Kanri, eine strategische Herangehensweise, mit der Optimierungsbemühungen effektiver auf die wesentlichen Problembereiche konzentriert werden können. Ferner wäre die Value Stream Analysis zu nennen, mit deren Hilfe die horizontalen Arbeitsströme über Abteilungen hinweg neu ausgerichtet werden können - denn diese Arbeitsströme sind es, welche die Werte erzeugen, für die der Kunde zahlt. Schließlich fallen in diese Kategorie auch A3 Thinking und Toyota Kata, mit denen sich die Anwendung einer wissenschaftlichen Denkweise auf allen Unternehmensebenen durchsetzen lässt. Diese und andere Werkzeuge in einer offenen, visuellen Umgebung zur Anwendung zu bringen, in der Schwierigkeiten und Widersprüche nicht unter den Teppich gekehrt werden, stellt für die in vertikalen Strukturen verhafteten deutschen Unternehmen eine besondere Herausforderung dar.
Beschreibung
Der Erfolg in der Praxis zeigt: Lean Thinking macht aus den einzelnen Unternehmensbereichen, die am Produktionsprozess beteiligt sind, ein hoch effizientes Netzwerk, das so dicht wie möglich am Kunden arbeitet. An zahlreichen Beispielen von erfolgreichen Unternehmen aus verschiedenen Kontinenten zeigen die Autoren, wie die fünf Grundprinzipien des Lean Thinking umsetzbar sind und wie man mit ihnen Produkte und Prozesse optimiert. In dieser neuen Auflage gehen die Autoren in einem exklusiven Beitrag auf die Erfolgsgeschichte von Lean Management in Deutschland ein.